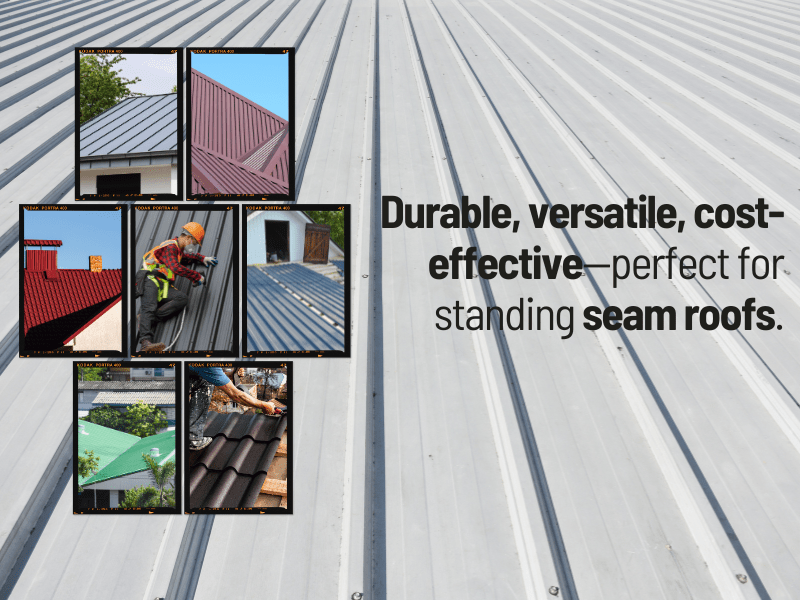
Mastering Structural Steel Fabrication: Key Methods and Best Practices
Home » Mastering Structural Steel Fabrication: Key Methods and Best Practices
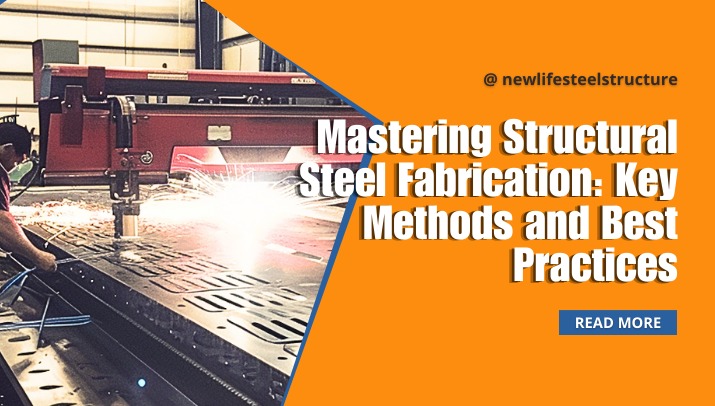
Structural steel fabrication is a critical process in construction as it transforms raw steel into predefined shapes and sizes to form the framework of buildings, bridges and other structures. This process involves various key methods which ensure the structural integrity and precision of the final product.
1. Cutting – Cutting is the first step in structural steel fabrication, where large steel sections are resized into required dimensions. Advanced techniques are employed in this phase which includes:
– Laser Cutting: Utilizes a high-powered laser beam to achieve precise with smooth edges in the cut.
– Plasma Cutting: Employs a high-velocity jet of ionized gas to slice through the steel efficiently and smoothly.
– Waterjet Cutting: Uses a high-pressure stream of water mixed with abrasive particles to cut through steel materials.
– Saw Cutting: Involves circular or band saws to efficiently cut the steel sections.
Each method offers different advantages and the choice of method depends on various factors like material thickness and desired precision.
2.Hole Making – Creating precise holes is important for assembling steel components. Drilling is commonly used for holes to install screws and rivets, ensuring high precision and minimal damage to the wall. While punching is suitable for thinner steel plates and non-circular holes, typically when the hole diameter is not less than the thickness of the steel. Drilling is generally preferred for its accuracy, while punching is used when material properties and design specifications permits it.
3. Bending – Bending is important for necessary angles and curves to steel components which is achieved through various techniques. Press Braking is one of the techniques which applies force using a press brake to bend steel into desired angles and roll bending involves passing steel through rollers to create curves and cylindrical shapes.
These methods allow for the creation of complex geometries essential in modern architectural designs.
4. Welding – Welding is fundamental in joining steel components to form a unified structure. The key welding techniques include two methods of welding. First is Shielded Metal Arc Welding (SMAW) which is also known as stick welding. It uses a consumable electrode coated in flux to create an arc that fuses the steel components. Another technique is Gas Metal Arc Welding (GMAW) which is commonly referred to as MIG welding and it employs a continuous wire electrode and shielding gas to produce a stable arc. Flux-Cored Arc Welding (FCAW) technique is similar to GMAW but utilizes a flux-filled wire electrode, eliminating the need for external shielding gas. Submerged Arc Welding (SAW) technique involves a granulated flux that blankets the welding area, protecting it from atmospheric contamination.
The choice of welding method depends on various factors such as material thickness, structural requirements, and working conditions.
5. Assembly – After individual components are fabricated, they are assembled to form larger sections or complete structures. This stage involves aligning and securing parts through bolting or welding to ensure dimensional accuracy and structural integrity.
6. Surface Treatment – To enhance the durability and aesthetics, fabricated steel undergoes through various surface treatments such as:
Painting: Acts as protective coating to prevent corrosion and provide a finished appearance.
Galvanizing: Involves coating steel components in molten zinc to make it corrosion-resistant.
Powder Coating: Involves electrostatically applying dry powder to the steel surface, followed by curing to form a durable finish.
These treatments are crucial for extending the lifespan of steel structures, especially in harsh environmental conditions.
7. Quality Control and Inspection – Throughout the fabrication process, rigorous quality control measures are implemented to ensure that the fabricated components adhere to safety standards and project requirements. Visual Inspections are done to identify surface defects and imperfections. Dimensional Checks are conducted to ensure components meet design specifications. Non-Destructive Testing (NDT) Methods such as ultrasonic testing, magnetic particle testing and dye penetrant testing are done to detect hidden flaws.
In conclusion, structural steel fabrication is a multifaceted process that demands precision and expertise. By using these key methods, fabricators can produce robust and reliable structures that form the backbone of modern infrastructure.
Recent Post
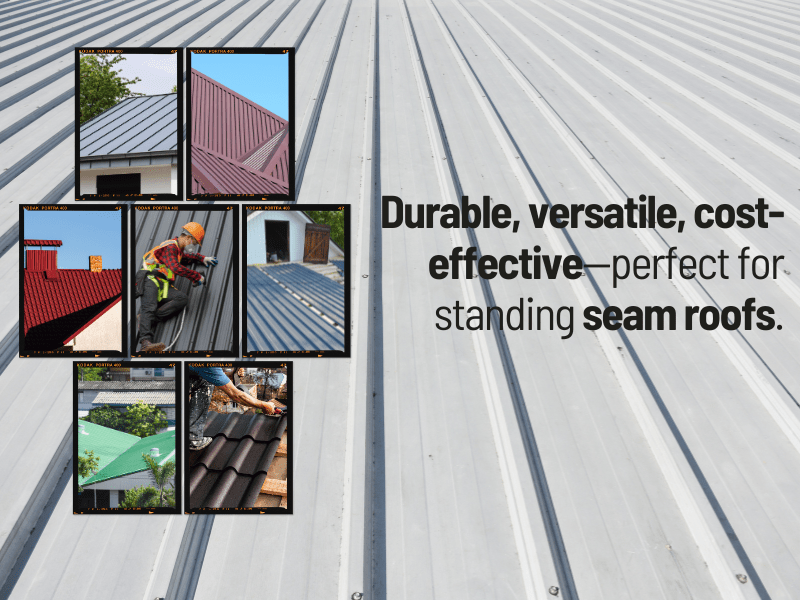
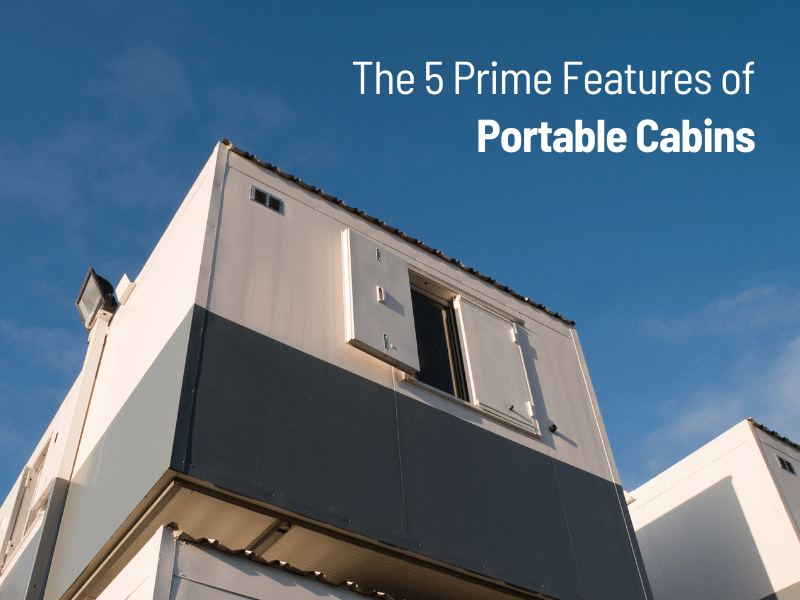
The 5 Prime Features of Portable Cabins
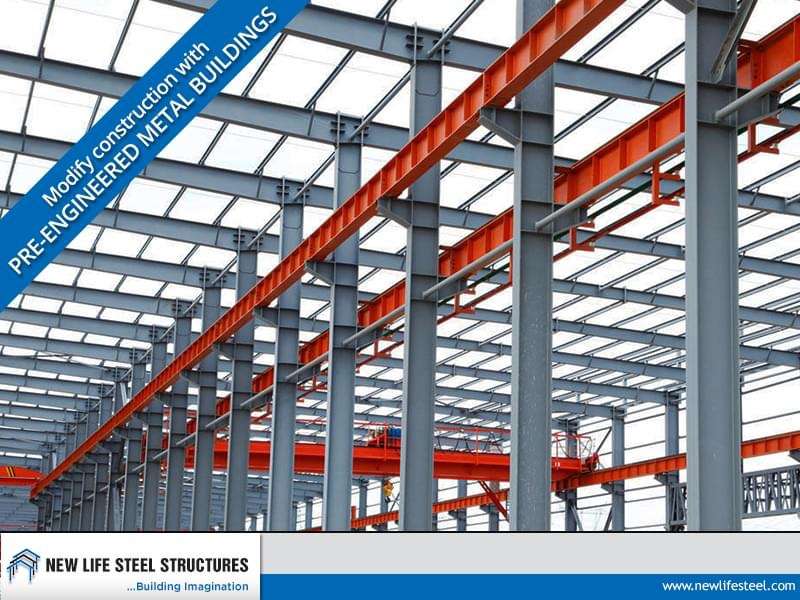